WEAV(3)D
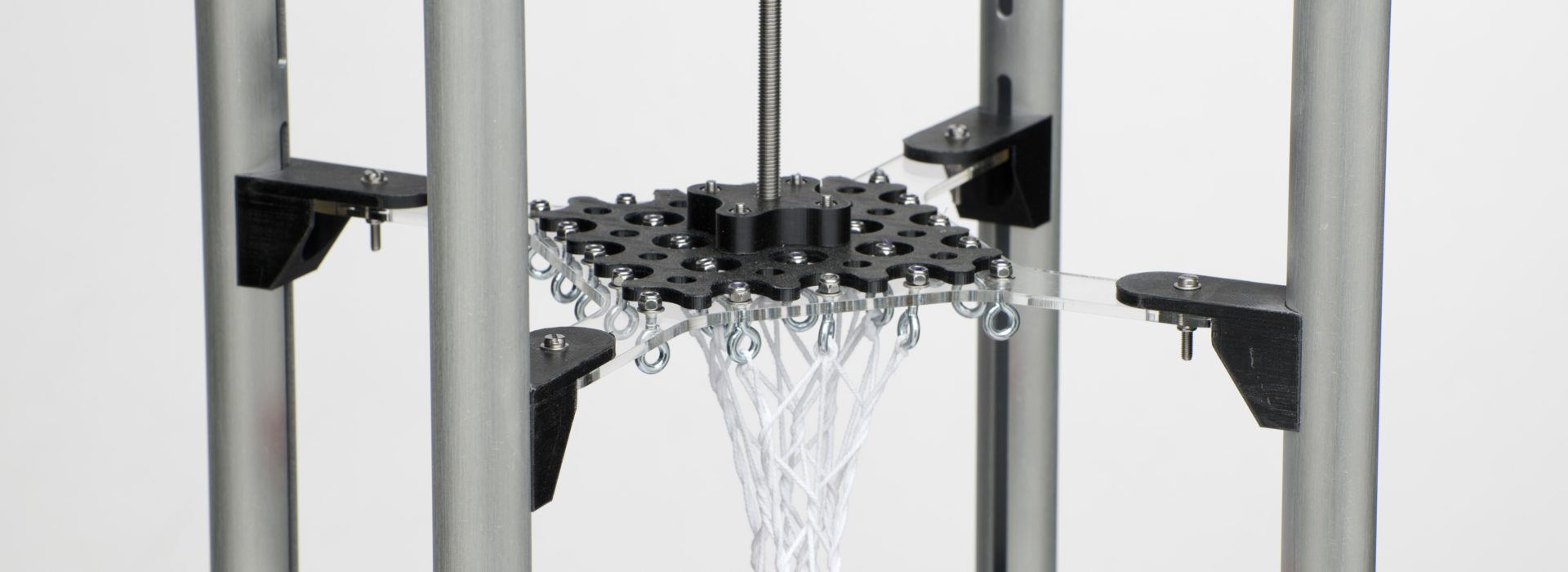
Can the shortcomings of digital manufacturing be remedied by taking inspiration from traditional craft techniques?
This question stemmed from my ongoing criticisim of the use of digital manufacturing techniques such as 3D printing and laser cutting in design. My criticism doesn’t revolve around the general use of these processes, but the long term effects they will have on the design landscape and consequently the consumers that commit design works to their homes.
Over the course of my period at WdKA, I have gained an awareness for the changing landscape of design. I have followed the trend towards an increased dependence on digital manufacturing techniques and have mostly relished in the advantages that they give. However, it took an intensely digital manufacturing skewed internship to force me to reflect on the position of these tools within the design and the delicate responsibility required whilst utilising them, especially in our climate conscious field. That responsibility being the act of conveying subtle lessons through the medium of the object on to the end consumer. Lessons ranging from material knowledge to a basic understanding of the process the object underwent. With traditional production methods, the process and material are often very apparent in the object, but with the advent of digital methods, this transparency of material and process is becoming more and more obscure, through the use of inaccessible processes and materials.
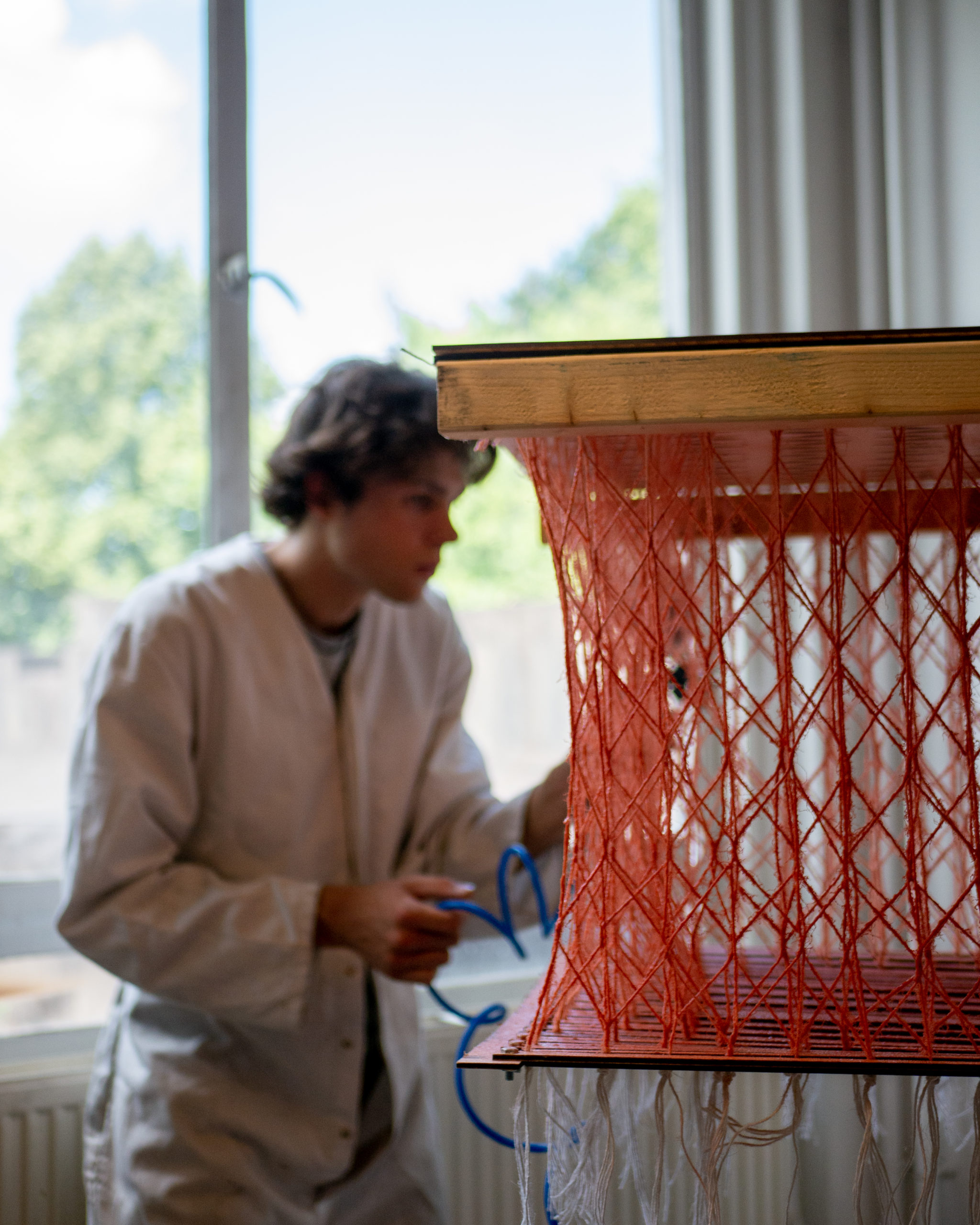
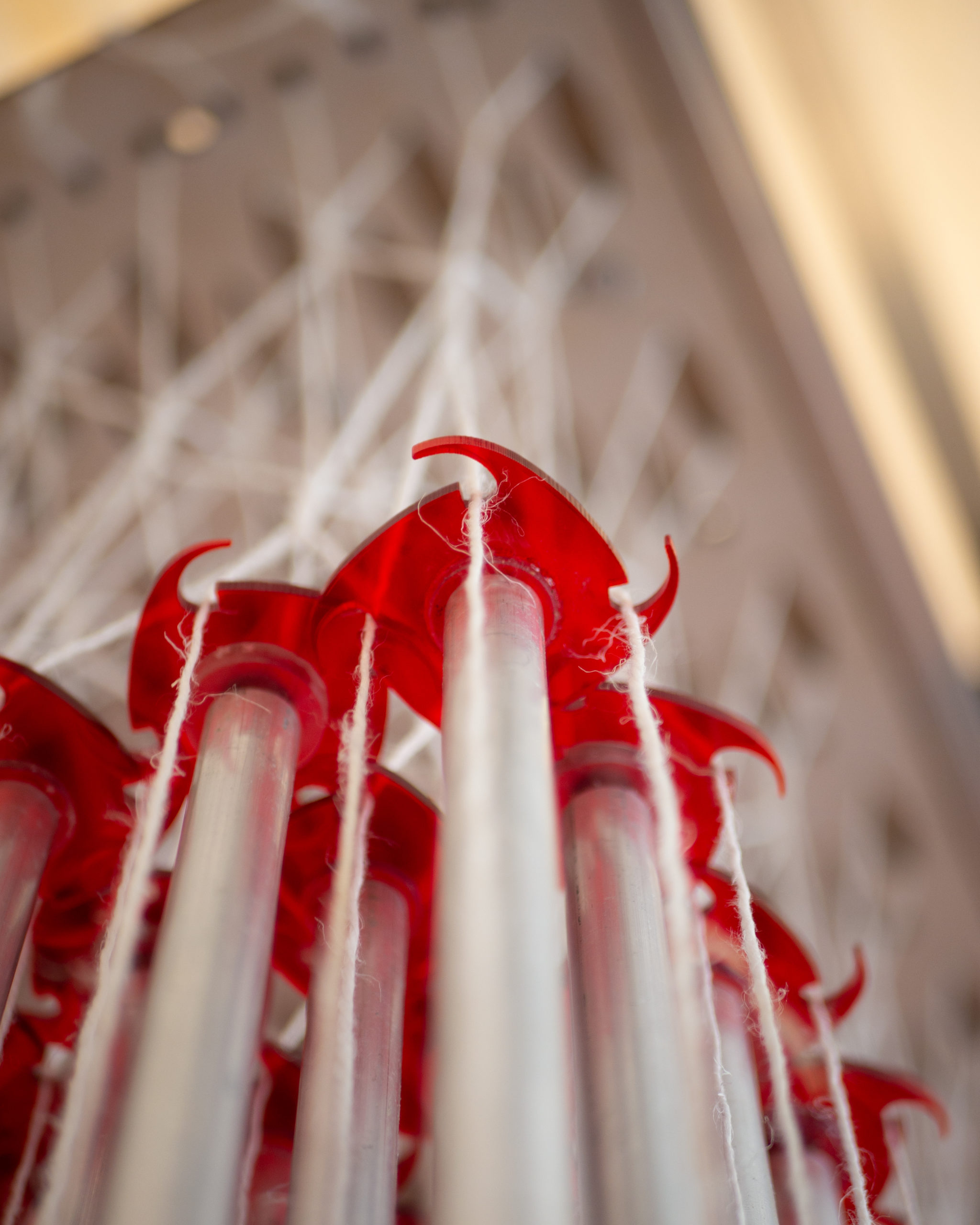
Our plan, from the very beginning was to make a statement advocating for a return to more traditional methods of crafting, which have this inherent visual story, that we believe will be sorely missed. We took the standpoint of confronting these digital processes by developing our own analogue process, that could compete with the likes of 3D printing, with the advantages of natural material, and the visual story that is created by making in a manual fashion.
This thought process resulted in the development of a 3D weaving process, heavily inspired by traditional weaving and knitting apparatus. We settled with a textile project, as it was clear to us that fibre would be the most accessible material that is widely available in all locations locally. There is also of course the ingrained knowledge surrounding textile processes that we would like to take advantage of a shallower learning curve between traditional weaving or knitting, and our process.
In the coming months we hope to take our process from the relatively small scale we have been working in, towards a more architecturally viable scale.
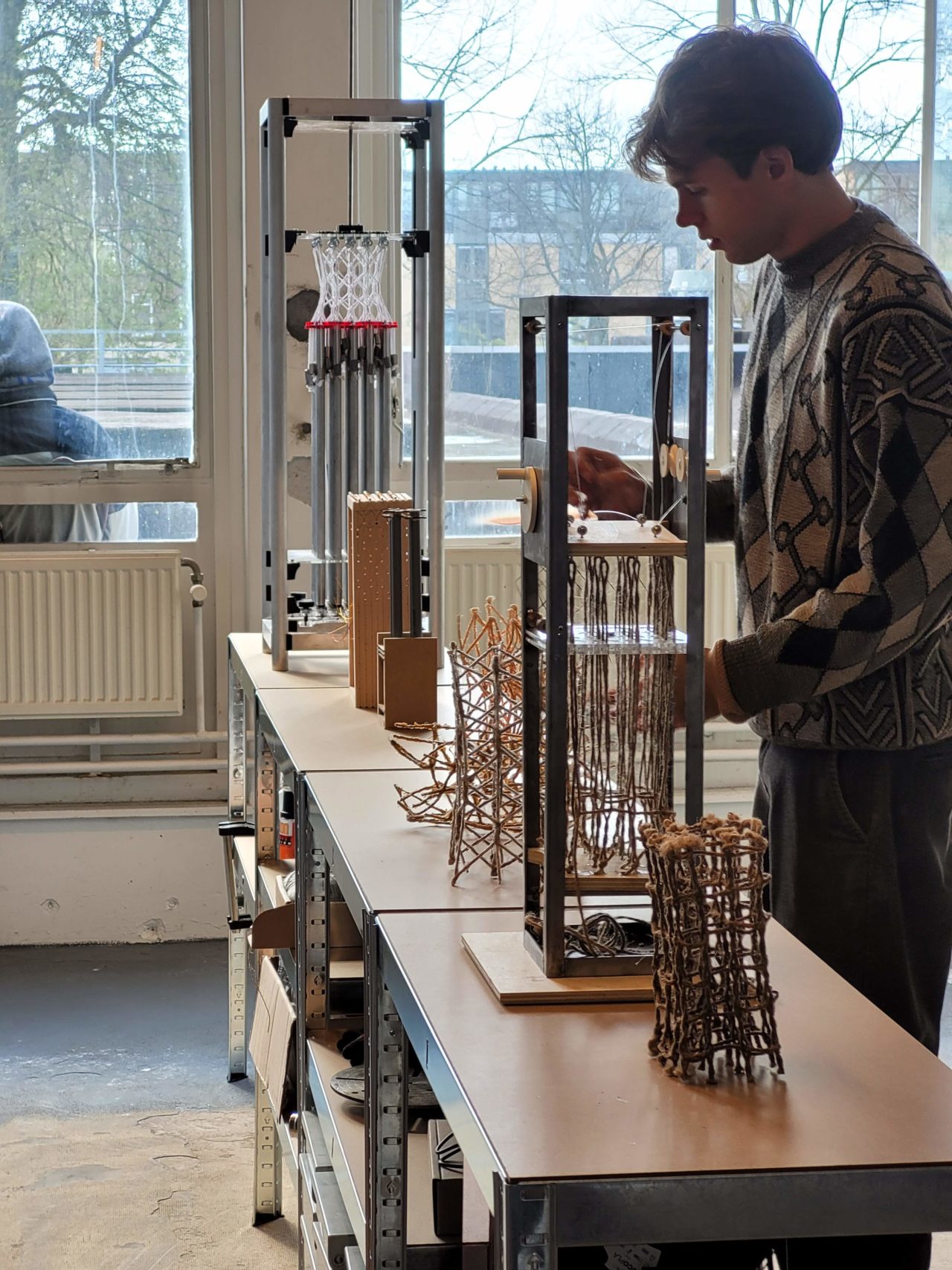
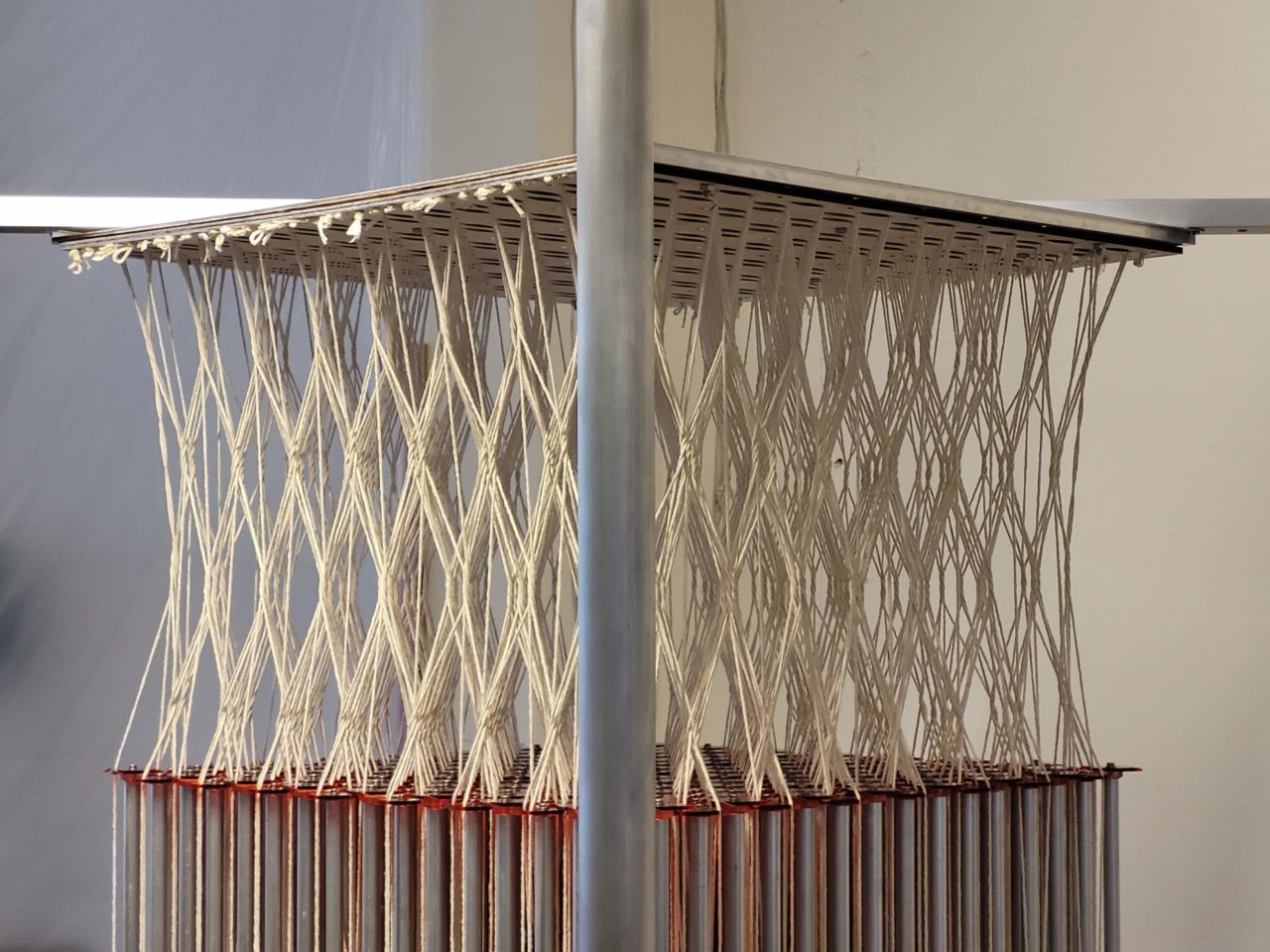
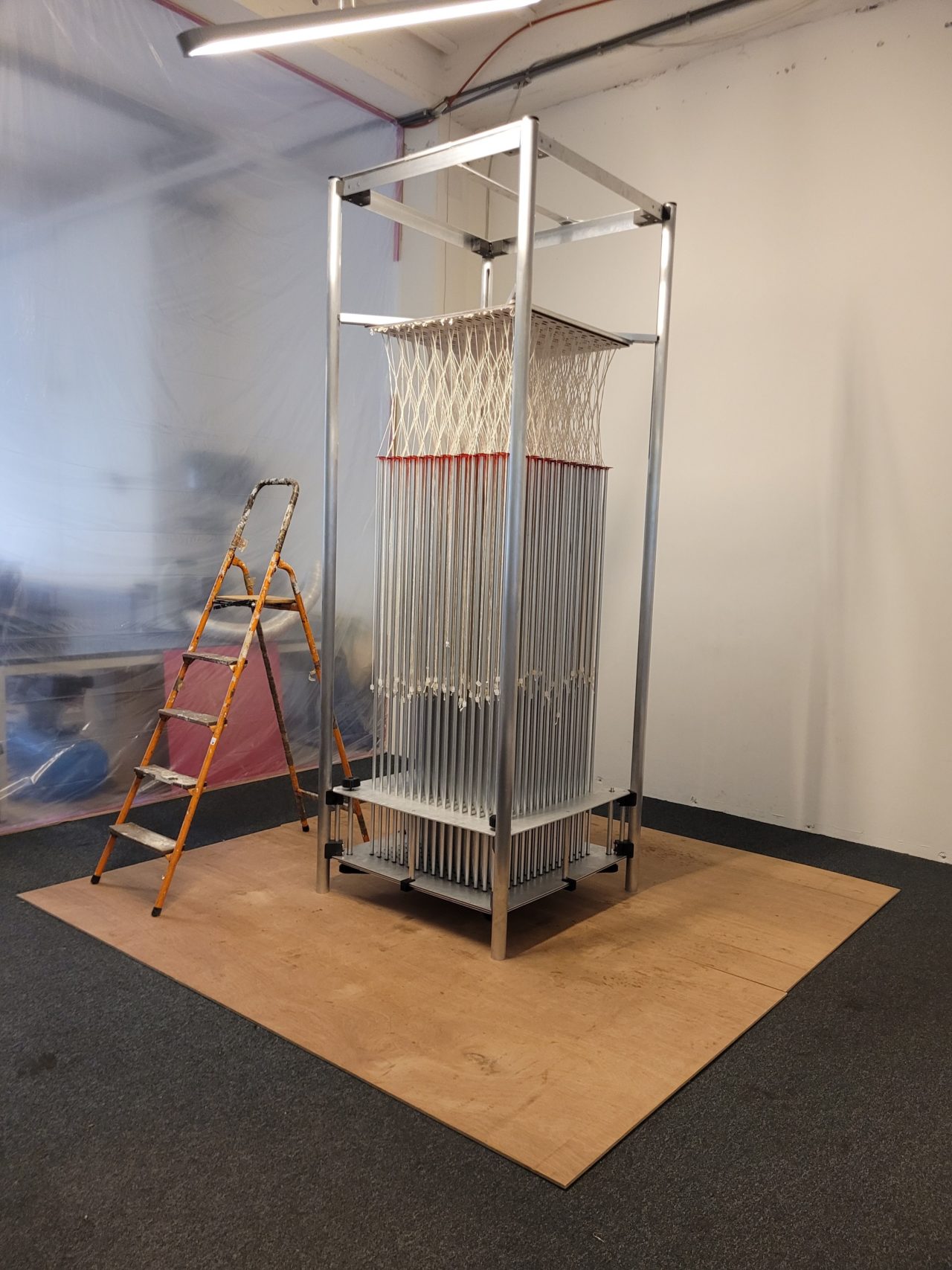